Touchscreens are used everywhere these days, from smartphones to tablets and PCs to interactive digital display screens. Most touchscreens are made from layered thin films of indium tin oxide (an inorganic, electrically conductive transparent material).
But both indium tin oxide and other inorganic materials of this kind have a disadvantage that one or the other reader has probably already experienced if a smartphone or tablet has been dropped: they are brittle and break easily. The solution to this one problem would be flexible and longer-lasting touch displays with the same electrical or optical properties. And it is precisely this solution that is presented to the readers of the current issue of "The Optical Society (OSA)" magazine by polymer scientists so-Young Park and A-Ra Cho from Kyungpook National University in Daegu, South Korea.
Co-polymer from organic materials
The two scientists have developed a process that produces a kind of so-called "hybrid" films composed of both inorganic and organic materials.
It started with a co-polymer composed of two organic materials (methyl methacrylate (MMA) and 3- (trimethoxysilyl) propyl methacrylate (MSMA) (poly (MMA-co-MSMA), MMA: MSMA = 78:22 molar ratio)), which are combined with another chemical substance trialkoxysilane. This co-polymer is then synthesized with two inorganic chemicals, titanium isopropoxide and tetraethyl orthosilicate to form hybrid layers with high (1.82) and low (1.44) refractive indices.
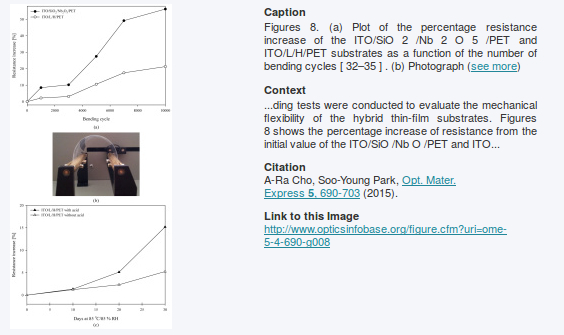
Results provide high optical transparency
Tests of the new hybrid films showed that both (both the high and low refractive index layers) are highly transparent. The H-materials on a glass substrate showed a high optical transparency of 96%, the L-materials on a glass substrate showed a high optical transparency of ~100%, both related to bare glass at 550 nm.
The new hybrid materials have been produced at low temperatures and without the use of a high vacuum, which ensures that production costs will be greatly reduced. In addition, the new process also enables the creation of multilayer films (e.g. films for anti-reflective coatings) with new application possibilities for different industries.
The results of the study can be downloaded as a PDF document at the URL given in our source.