ULTRA touch screens are used directly on the assembly line
Yesterday, the new Volkswagen plant in Chattanooga was opened. There, 2,000 employees will build over 150,000 vehicles per year. This figure is even more impressive when broken down into the number of vehicles produced per day or hour. That's 411 per day or 17 vehicles per hour. It is more than understandable that a production standstill must be avoided at all costs.
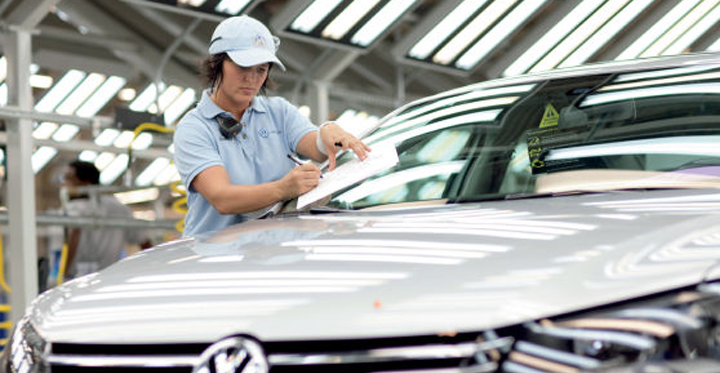
Every production stop costs immense sums of money
Our ULTRA touchscreens are used directly on the assembly line at the VW factory in Chattanooga to minimize production downtimes. The environment is very demanding, because in order to achieve high productivity, a very high degree of automation is absolutely necessary. ULTRA GFG touchscreens are an excellent choice here, because the visual and flexible display reduces training costs and supports intuitive operation.
Only our ULTRA touchscreen technology met all requirements
The combination of uncompromising operating safety and the robust, patented glass film glass structure were convincing arguments for the use of our technology. Resistive technology was a mandatory prerequisite to ensure operating errors, especially in such a demanding environment. The increased impact resistance of our ULTRA touchscreens was also an additional benefit that I did not immediately identify for this application.
I was also a bit surprised by the impact resistance requirements, because when you think of high impact requirements, the first thing that often comes to mind is unguarded kiosk applications and vandalism. Both prerequisites, I thought, are not met in a high-tech plant. But the problem of impact resistance was caused by free-swinging pneumatic screwdrivers. If the worker hands over the screwdriver at an awkward angle, the impact wrench swings back to the touch screen in the PanelPC. So far, this has ended either with the breakage of the touchscreen base glass or a deep scratch in the polyester. Sometimes there was also a dent in the PET, which often led to a permanent tripping and made the touchscreen unusable. The scratches greatly reduced the readability and lifespan. Our patented GFG technology reduced the formation of scratches and dents and significantly increased the absorption of the impact force.
The cheapest ULTRA touchscreen version was sufficient
Even the standard version of our ULTRA touchscreens easily met both requirements. The standard variant absorbs an impact energy of approx. 1.5 joules. For higher requirements, we offer the C3 construction with a 3mm thick chemical tempered glass on the back. This structure then creates approx. 5+ joules, which corresponds to the impact energy of a 0.5kg steel ball from a height of 1m.