In April 2015, the Korean Institute of Electronic Technology (KETI) announced the production of an ultra-thin OLED electrode material for mobile devices. The special feature of this electrode material is that it is able to retain its electrical properties even after more than a thousand bending processes.
According to the institute, the OLED electrode material should enable the production of smartphones, for example, that can be rolled or completely folded like paper. Mass production is currently being discussed with major chemical materials manufacturers from Korea. It is planned to make these fully foldable smartphones available for commercial scale within the next two years.
ITO too costly and inflexible
Until now, indium tin oxide (ITO) has been an important "ingredient" in these products for the touchscreen display in smartphones and tablets. This is because ITO-based touchscreen displays are characterized by excellent brightness and conductivity. However, since ITO brings with it numerous disadvantages for novel technology products - such as expensive manufacturing costs and brittleness of the surface - it is no longer an option for the planned new technologies.
Today, the focus is increasingly on the use of electrode materials based on silver nanowire. This is because this material is more suitable for flexible OLED displays.
Silver nanowire well suited for mass production
The Korean KETI Institute uses silver nanowire as an "input" on a polymer substrate for its planned mass production and then adjusts the surface roughness by means of plasma radiation in order to obtain an acceptable efficiency level similar to ITO-based OLED displays.
ITO versus silver nanowires
Compared to indium tin oxide (ITO), several factors speak in favor of the use of silver nanowires (SNW).
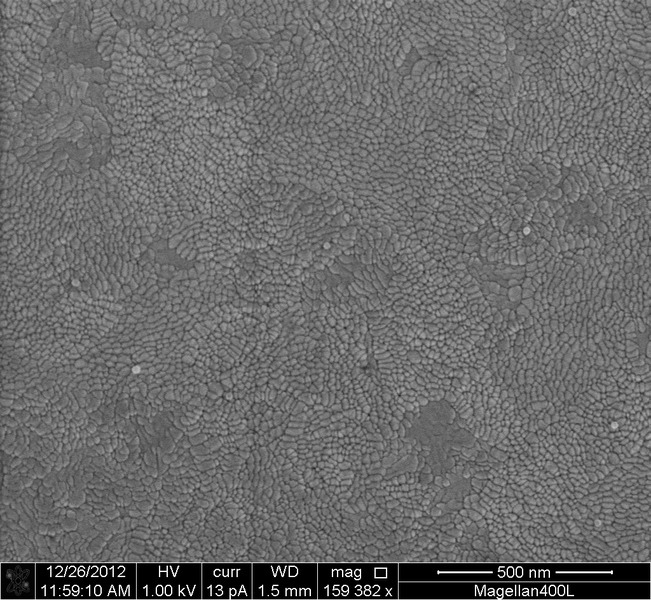
The new Touchs products with this material are lighter, thinner, responsive and, above all, more cost-effective to produce. In addition, they provide excellent flexibility, as well as high light transmission. Since, depending on the manufacturing process, hardly any or no chemicals are used that have to be disposed of at great expense, a more environmentally friendly production process is also possible than with ITO materials.
Products equipped with non-ITO-based transparent conductors are of increasing interest to the market. More information on the planned project of KETI can be found on the institute's website at the URL given in our reference.